In today’s dynamic manufacturing landscape, discovering the appropriate technology for your plastic injection molding service can make all the effect for your company. As companies strive for efficiency, quality, and affordability, understanding the various choices available in plastic molding technologies is imperative. The optimal choice not only determines manufacturing pace and quality of goods but also profoundly affects your overall cost structure and market standing.
Investing in the suitable injection molding technology is a tactical decision that can yield significant returns. With innovations in plastic science and engineering, the choices available today provide more versatility and accuracy than ever prior. Regardless of whether you are aiming to create small components or big industrial parts, a thorough knowledge of these technologies will direct you in choosing a service that meets your particular needs and helps your enterprise flourish in a swiftly evolving market.
Understanding Injection Molding Methods
Injecting molded parts is a manufacturing method that involves producing plastic parts by injecting molten plastic into a mold. This technique is widely used due to its capability to create large quantities of parts with great accuracy and uniformity. The key components of the injective forming equipment include the injection system, the clamping system, and the mold alone. Grasping these elements and their roles is essential for choosing the appropriate technology for your polymeric injection molding operation.
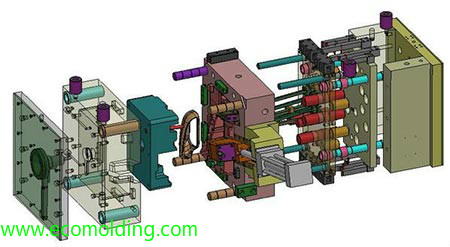
There are multiple types of injection molding technologies that cater to varied production requirements. Traditional injection molding is the predominant method, ideal for creating mass amounts of uniform parts. In contrast, technologies like gas-assisted injection molding and multi-material injection molding provide creative answers for particular applications, allowing for lighter parts or the combination of different plastics. Evaluating these various methods aids businesses identify the most effective approach based on their manufacturing requirements and desired outcomes.
Additionally, developments in injection molding technologies have resulted in increased efficiency and minimized waste. Techniques such as injection molding with reclaim materials or using biodegradable plastics contribute to eco-friendliness efforts while maintaining high performance. By staying informed about these advances, businesses can make knowledgeable decisions that correspond to both their production goals and environmental responsibilities, guaranteeing they invest wisely in their polymeric injection molding operation.
Considerations to Consider When Opting for a Provider
When picking a plastic injection molding service , the first factor to consider is the provider's expertise and standing in the industry. Companies that have been in the business for a significant amount of time often have a established background and a portfolio that showcases their skills. Researching customer feedback and case studies can give you clues into how reliable and effective the service is. A well-established provider will probably have the knowledge to handle different project complexities and issues, ensuring that they provide high-quality results regularly.
Another, important consideration is the tools and machinery used by the injection molding provider. Modern machinery and processes can significantly influence the standard and precision of the molded components. Look for providers that commit in modern technology, as this often leads to better product outcomes, quicker turnaround times, and better cost-effectiveness. Understanding the specific molding methods and advancements being utilized can help you ascertain if the service meets your project requirements and business standards.
Cost is always an important element, but it cannot be the only determining factor. It's crucial to consider affordability with quality and service. Request comprehensive quotes from various injection molding services and compare the value offered, including post-production support and customization options. Be wary of quotes that seem too low, as they may imply compromises in standards or service. Ultimately, selecting a trustworthy plastic injection molding service will pay off in the long run through improved product performance and commercial success.
Cost-Benefit Analysis of Plastic Injection Molding Options
In the process of considering a plastic injection molding service, it is important to evaluate the expenses versus the prospective benefits. The initial investment for injection molding machinery and installation can be considerable, but when spread over high production runs, the per-unit cost significantly reduces. Understanding the volume of production required to validate the expenditure is essential. For businesses with high demand for consistent parts, this can result in substantial savings and productivity.
In addition to initial costs, one must assess the operational costs associated with different injection molding technologies. Conventional machines may have reduced initial prices, but they often come with elevated energy and maintenance overheads. In contrast, newer technologies, such as electric injection molding machines, may have a higher purchase price but offer lower operational costs through energy conservation and reduced production halts. Evaluating these variables can lead businesses toward a more sustainable and cost-effective solution over time.
Finally, it's important to consider the quality and versatility. Sophisticated injection molding solutions can manufacture parts with tighter tolerances and detailed designs that may not be realizable with legacy methods. Putting resources in the appropriate technology can not only improve product quality but also allow for a wider range of applications. This adaptability can open additional market opportunities and finally contribute to a better return on capital. Conducting a detailed cost-benefit will help companies choose the optimal option that fits with their long-term business goals.